Topics > Wellhead & Environment
Blowout Preventer
09/05/2016
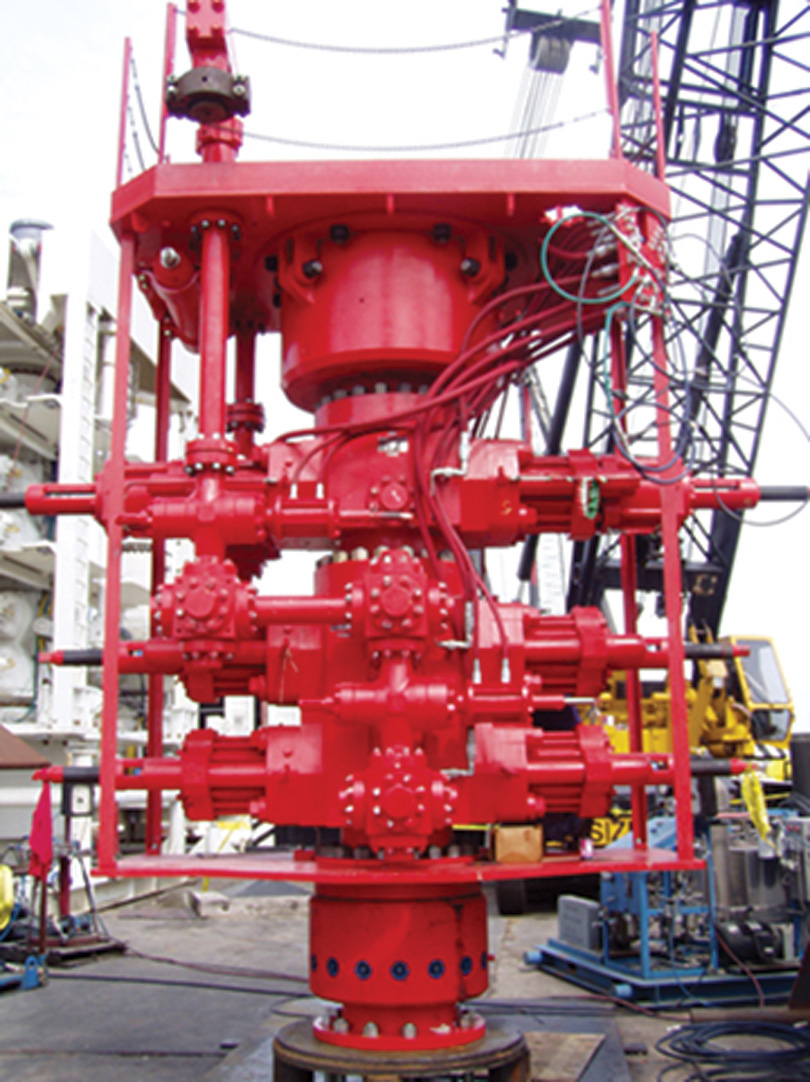
Whole BOP Operation Systerm
2. Annular blowout preventer
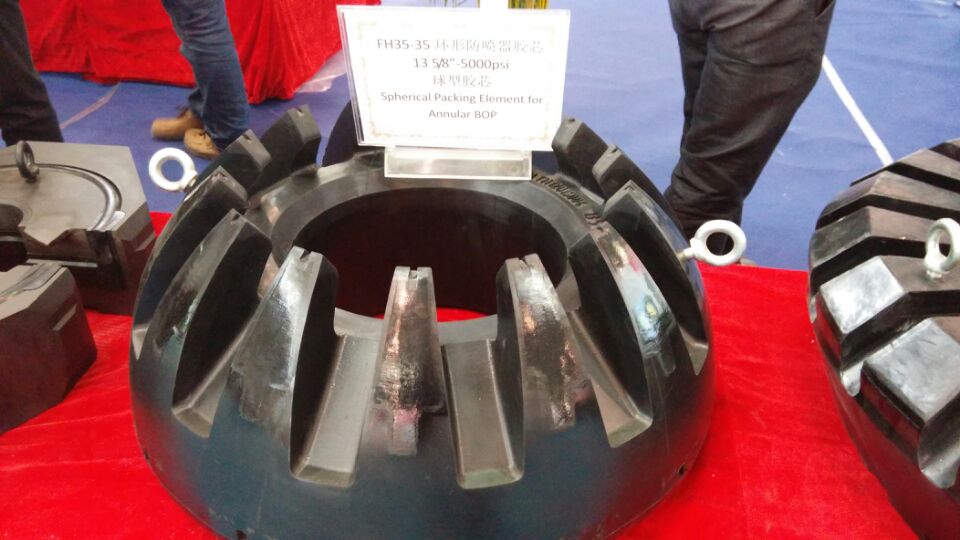
Annular BOP using the conical packing element
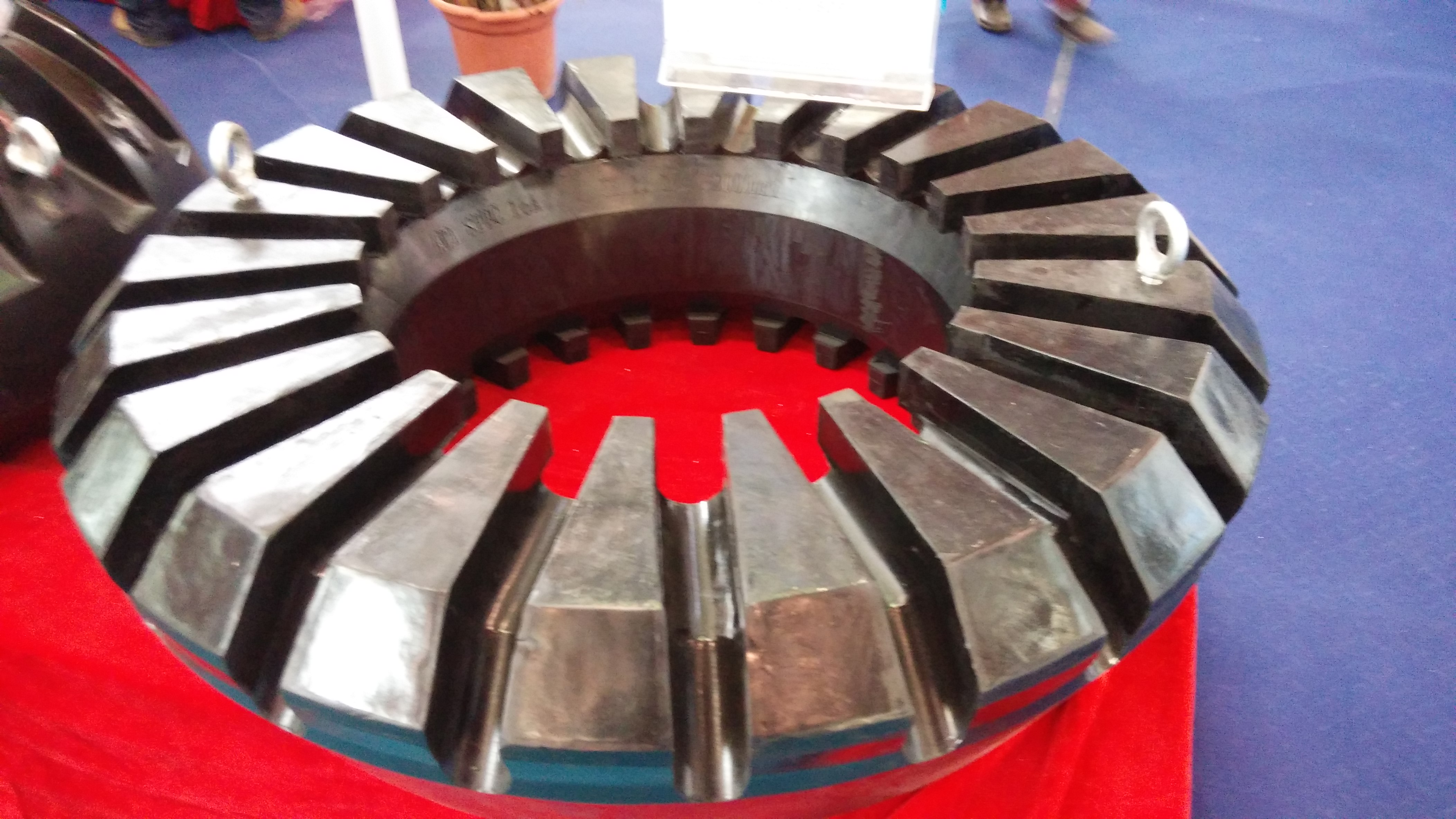
Annular BOP using the Combined packing element
Products
+APR Drill Stem Testing Tools
- Rupture Disk (RD) Sampler
- Slip Joint
- Hydraulic Jar
- Shock Absorber
- Gauge Carrier
- Drain Valve
- OMNI Valve
- LPR-N Valve
- Safety Valve
- Safety Joint
- Circulating Valve
- RTTS Packer
- Super Safety Valve/Subsea Safety Valves (
- Hydro Trip Pressure Sub
- Surface Well Testing system
- APR Pressure-controlled Formation Tester
- Full-bore Compensating Pipe
- Retrievable Service Packers
- Fullbore DST string
- DST TOOLS specification
- Subsurface Control Valve (SSC) Storm Vavl
- Champ v Packer
- Storm Valve
- Tester Valve
+Drilling Equipment
- Casing Scraper
- balck rhino Non rotating Casing Scrappe
- RazRdillo Casing Scraper
- multiple activation autolock bypass tools
- Non-rotating wellbore casing scraper
- Wellbore Cleaning up tools
- Drill Pipe
- Downhole Motor
- KINGWELL Stabilizer-sleeve type
- Deflecting tools and mill tools
- drill bits
- Cross Coupling Cable Protector
- KINGWELL Underreamer
- Reammate Underreamer
- mill shose
- KINGWELL Raiseboring drill pipes
- Stabilizer
- future drill tools
- RGS Remote Gauge Stabilizer
- Shock Tools
- Casing and Pipe cutting equipment
- HORNET Series Drilling Tools
- Hydraulic Oscillator
- Hydraulic Thruster
- Drill Bit
- Jar Intensifier Type YJQ
- Overshot
- Full opening safety valve
- Top Drive Drilling Tools
- Hole Opener
- Drill Hydroscillator
- Lubricated Fishing Bumper Sub Type BXJ
- Drilling Jar
- Continuous Circulating Valve
- Inside Blowout Control Tools
- Multi-cycle Circulating tools
- Hydraulic Jar Type YSJ
- Drilling Accelerator Type ZJQ
- Fishing Bumper Sub Type KXJ
- Model DJQ Cable Jar
- Model ZTX Highly-Efficient Vibration Resi
- Super Fishing Jar Type CSJ
- Surface Bumper Jar Type DJ
- Surface Bumper Jar Type DX
- Two-action Drill Accelerator Type SZJQ
- Fishing Spear
- Junk Basket
- Wear Preventive Subs
- Kelly
- Heavy Weight Drill Pipe
- Drill Collar
- Magnetic Fishing Tool
- Die Collar
- Casing Scraper
- Shock Absorber
- Pup Joint
- Subs
+Rig Accessories
- KWDWS Water Cooling Eddy Current Brakes
- BOP
- Christmas Tree
- An Overview of OCTG Piping Inspection Met
- Casing and tubing
- Wire-wrapped Screen
- ASTM A53 GRADE B SEAMLESS
- flange
- EN 10217 Welded steel pipe
- Oil Country Tubular Goods (OCTG)
- ASTM A333 Grade1 Carbon Steel Pipe
- Coiled Tubing
- High Pressure Fluid Control Products
- Coupling
- API 5CT Hot Rolled Tubing Pup Joint
- Ram Type and Annular Type Blowout Prevent
- Solids Control System
- Crown Block
- F-1600HL Mud Pump
- Coiled Tubing BOP
- drilling line
- Kill Manifold and Choke Manifold
- F-2200HL Mud Pump
- Ironroughneck
- Hydraulic Disc Brake System
- Mud Hopper and Mud mixing pump
- Gate Valve
- Top Drive
- OCTG
- Butterfly Valve
- Globe Valve
- Ball Valve
- Plug Valve
- Choke Valve
- Check Valve
- Casing Hanger and Tubing Hanger
- Tubing Spool and Casing Spool
- Slip
- Tong
- Elevator
- Tubing Head
- Casing Head
- Drawworks
- High and Low Pressure Pipe Manifold
- Forgings for Flange/Valve/Shaft/Gear
- Forging for Downhole Tools
- Pipe Mould
- Die Steel/Tool Steel
- Mandrel Bar
- Rolling Mill Roll
- Corrugated roll
- Travelling Block and Hook
- Rig Swivel
- Drilling Rig Mast
- Rotary Table
- Mud Pump
- Vacuum Degasser
- Other Solid Control Equipment
- Shaker Screen
- Submersible Slurry Pump
- Shear Pump
- Mud Agitator
- Centrifugal Pump
- Decanter Centrifuge
- Desilter
- Desander
- Mud Cleaner
- Linear Motion Shale Shaker